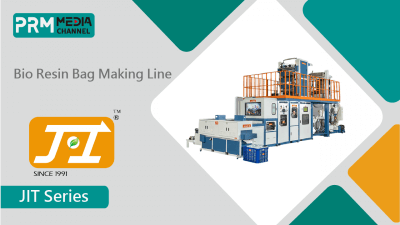
Bio Resin Bag Making Line - JIT Series | JANDI’S
JANDI'S INDUSTRIAL CO., LTD. is committed to developing blown film machines combined with bag making, printing, and recycling machines. Until 2018, they obtained more than 30 patents of plastic machinery in China and Taiwan. With the concept of plastic reduction raising, JANDI'S proposes an idea about green innovation. The company develops JIT series integrated plastic bag making machines that are 100% suitable with biodegradable and compost materials such as PBAT and PLA. Moreover, JANDI'S added the automatic packaging part to JIT series.
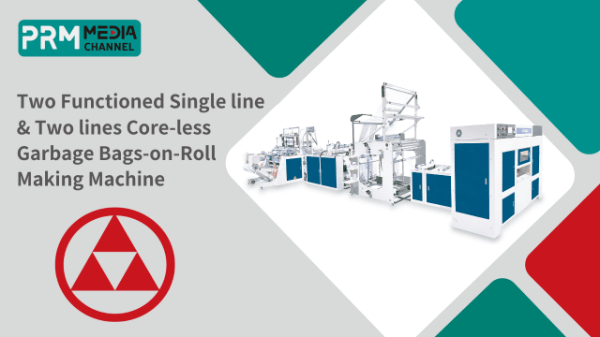
Two Functioned Bags on Roll Making Machine:SR(2)MR(1)-1000-OS-2T-R4S | COSMO
Fully Automatic High Speed Two Functioned Single Line & Two Lines Core-less Garbage Bags on Roll Making Machine Machine Model : SR(2)MR(1)-1000-OS-2T-R4S Machine Name:PHENIX • Core-less bags on roll • star sealing bags / Bottom sealing bags with V, C, N, M shape • Shuttle sealing & feeding system • Four shafts re-wind system
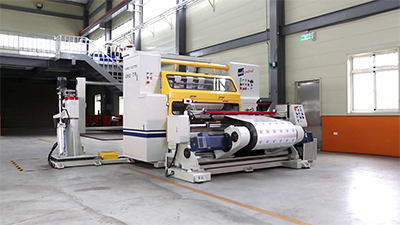
UHS Turret Slitter Rewinder - UHS-TR | WEBCONTROL
UHS Turret slitter rewinder The UHS-TR model is a proven fully automatic slitter rewinder, offered with many options to fulfill even the most demanding applications: - Cutting-edge slitting systems - Reliable auto cut and transfer - Advanced tension control - Combined with progressive differential winding technology - Precision and capacity at an affordable cost. - UHS-TR a must addition to any plant requiring quality Automatic knife positioning down to 25 mm slit width, double turret unwind, automated finished roll unloading systems are some of the available options to increase productivity, quality and decreasing operator influenced down time. Materials to be processed: Plastic film, paper and laminates Thickness range: -Rigid films: 10 – 200 micron -Soft films: 12 – 300 micron Machine Specification - SLIT UHS TURRET: -Web width:1300 / 1600 mm max -Unwind roll diameter: 1000 mm -Unwind roll weight: 1500 kg -Unwind roll cores: 3” and 6” I.D. -Finished roll diameter: 610 mm max -Finished roll cores: 3” and 6” I.D. -Slit width: 50 mm and up -Machine speed max: 600 m/min (depending on material type/quality) -Winding tension: 0.5 pli to 2.5 pli (11 - 45 kg) standard
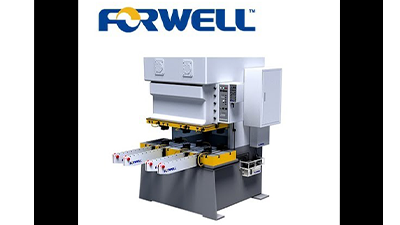
Quick Die Change System | FORWELL
Forwell’s Quick Die Change System is an automatic die changing system that can be specifically designed for hydraulic and mechanical power presses and press production lines. This system automates the die changing process and provides increased speed, efficiency and productivity to a workshop. The Quick Die Change System not only reduces die change time, but also promotes diverse small batch production runs and streamlines production management.
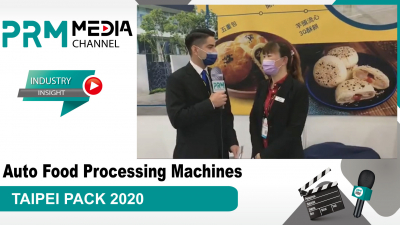
Food Processing Machine Solutions | HUNDRED MACHINERY
Since 1996, Hundred Machinery Co., Ltd. has been the professional automatic encrusting machine manufacturer in Taiwan. PRM Media Channel had an interview at the recent TAIPEI PACK and had a chance to introduces the companies automatic food processing machinery lines. Let us know your opinion and the inquiry in the comment section. Stay tuned for the forthcoming interview videos and remember to subscribe to our social media channels for similar videos!~ MAIN PRODUCTS/SERVICES OF HUNDRED MACHINERY:
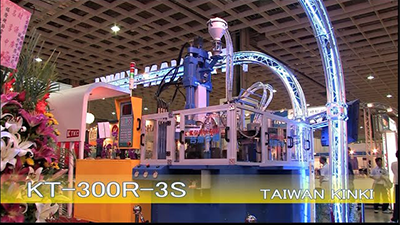
Vertical Injection Molding Machine Rotary Table | TAIWAN KINKI
MACHINERY IN THE VIDEO: Vertical Injection Molding Machine -Rotary Table KT 300R 3S FEATURES: -Vertical mold clamping and injection, small footprint, and high degree of precision. This machine is ideal for the injection of medium and small products with inclusions. -The Dual-cylinder injection system offers high injecting pressure for fast operation, making this injection machine your best choice for the production of thin items. -Direct-pressure mold clamp allows even injection force, and the relatively low pressure means maximum precision and an incredibly smooth cycle of operation. -Choose a platen or a rotary plate in accordance with the type of products to be injected, in order to achieve the best possible in feed and injection effects. -This machine offers a wide range of programmable functions including automatic inclusion, extraction, and fully-automatic production.
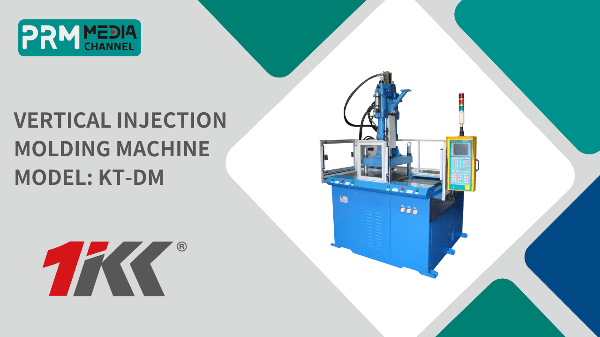
Vertical Injection Molding Machine - KT 300 | TAIWAN KINKI
FEATURES: 1.Vertical mold clamping and injection, small footprint, and high degree of precision. Our Vertical Injection Moulding Machine is ideal for the injection of medium and small products with inclusions. 2. Direct-pressure mold clamp allows even injection force, and the relatively low pressure means maximum precision and an incredibly smooth cycle of operation. 3.KT-300 Vertical Plastic Injection Molding Machine offers a wide range of programmable functions including automatic inclusion, extraction, and fully-automatic production. 4. Dual-cylinder injection system offers high injecting pressure for fast operation, making this injection machine your best choice for the production of thin items. 5. Choose a platen or a rotary plate in accordance with the type of products to be injected, in order to achieve the best possible in feed and injection effects. 6. There are also many other control systems that facilitate flexible production and keep costs low while maximizing precision.
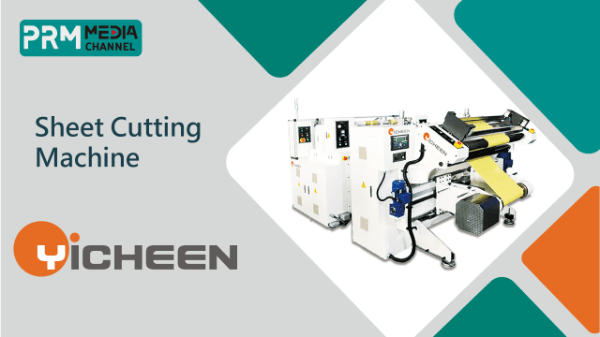
Sheet Cutting Machine | YICHEEN
Description: Friendly interface, PLC computer touch-panel screen control system. Non-hydraulic design, no pollution, low noise, best for using in dustless room. Servo motor control feeding (for EVA sheet cutting tolerance +/-1mm). Modulating control for tension control, it keeps cutting stable. Anti-static PU roller drive for reducing scrape happened. Optional devices: Shaftless unwind stand (electrical left/right moving), EPC (Edge Position Controller), Slitter, Punching device (electrical left/right moving), Automatic stacker, Static eliminating device,
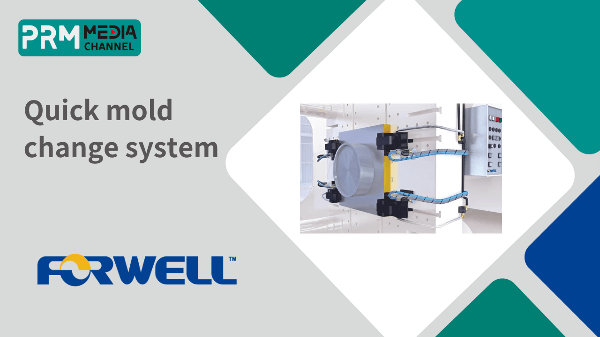
Quick mold change system|QMCS|for Injection molding|Sistemas de cambio rápido del molde|FORWELL
Forwell has been a pioneer of Quick Mold Change Systems for many years. With over 20 years of experience in developing these systems they can offer you the best for your molding operations. These fully customizable Quick Mold Change Systems drastically minimize setup times, maximize efficiency and increase safety. Forwell’s Quick Mold Change System can be designed to fit almost any injection molding machine and mold casting machine to allow for quicker mold change times, resulting in shorter machine down time and increased productivity. This system uses a special mold clamp that does not require a cut out on the mold, increasing its application versatility and allowing it to be used with a large number of different molds. Quick Mold Change Systems can rapidly transform your workshop, allowing for easy changeover for small batches, reduced labor costs and reduced stock holding. Coupling this system with a Mold Cart System will allow for fully automatic mold changing, further increasing the efficiency and productivity of your manufacturing operations. When installing a Quick Mold Change System for your injection molding and mold casting operations there are a number of direct and indirect benefits. Review the following table to see an overview of all of these benefits. Indirect Benefits Die Standardization Press Standardization Increased Safety Improved Working Environment Increased Competitiveness Direct Benefits Reduction in Die Change Time Efficient Small Batch Runs Reduced Stock Handling Higher Productivity and Quality Reduction in Labor Costs
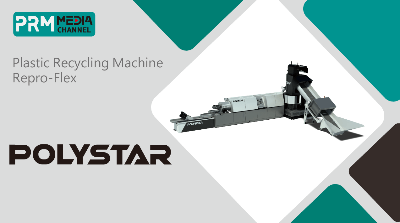
Plastic Recycling Machine, Repro-Flex | POLYSTAR
【Machine Features】 The one-step plastic pelletizing machine, Repro-Flex, combine cutting, extrusion, and pelletizing into one compact and efficient pelletizer line. The cutter-compactor of the plastic pelletizing machine prepares the plastic waste (PE plastic film and PP plastic film waste) into an ideal condition for the extrusion process and feeds the plastic waste directly into the extruder. This integrated system does not require a separate crusher, and therefore, eliminates the problem of inconsistent feeding, reduces space and labor costs, and has lower energy consumption. Simple in Design. Flexible in Operation. POLYSTAR is able to customize its machines regarding customers’ needs. How this pelletizing system works: 1. Feeding a. By belt conveyor Feeding of scraps is easy and automatically controlled depending on the amount of material input. b. By Nip roller Film-on-rolls can be fed at the same time. 2. Cutting and compacting The cutter compactor integrated cuts, dries, and compacts the material which enables a fast and stable feeding from the compactor directly into the extruder. 3. Degassing system The two-zone degassing can process plastic film with larger printed areas. 4. Filtration Screen change with a dual channel system for non-stop operation that also prevents plastic material from leaking. 5. Pelletization Water-ring pelletizing system, also known as hot die face pelletizing, the plastic comes from the recycling extruder and is directly cut by the rotating knives attached to the surface of the die head. 6. Final Product Round-shaped recycled pellets are produced and cooled inside the water ring immediately. 【Company Intro】 Headquartered in Taiwan, POLYSTAR has focused on the user-friendliness of its machines through continuous re-engineering, making recycling extremely “Simple” for its users – Easy operation and maintenance is what makes POLYSTAR the No.1 selling recycling machine today. Over the past 32 years, more than thousands of POLYSTAR recycling machines have helped worldwide plastic producers to reprocess their post-industrial (in-house) waste back into high-quality pellets in a simple and easy way.
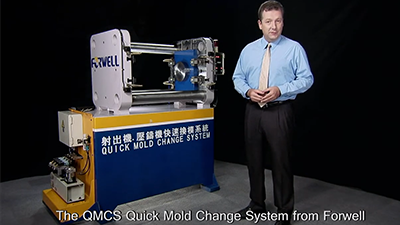
Quick Mold Change | FORWELL
Quick Mold Change - Quick Mold Change System-forwell-qmcs-en-Forwell Features • Decreased mold change time • Fully customizable to fit a wide range of machines • Safer operations • Reduced labor costs • Easy changeover for small batch runs System Introduction : Forwell has been a pioneer of Quick Mold Change Systems for many years. With over 20 years of experience in developing these systems they can offer you the best for your molding operations. These fully customizable Quick Mold Change Systems drastically minimize setup times, maximize efficiency and increase safety. Forwell’s Quick Mold Change System can be designed to fit almost any injection molding machine and mold casting machine to allow for quicker mold change times, resulting in shorter machine down time and increased productivity. This system uses a special mold clamp that does not require a cut out on the mold, increasing its application versatility and allowing it to be used with a large number of different molds. Quick Mold Change Systems can rapidly transform your workshop, allowing for easy changeover for small batches, reduced labor costs and reduced stock holding. Coupling this system with a Mold Cart System will allow for fully automatic mold changing, further increasing the efficiency and productivity of your manufacturing operations.
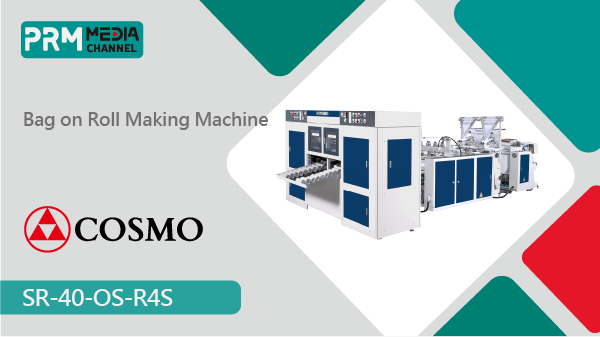
Bag on Roll Making Machine | COSMO
COSMO has many years of experience in bag making machines. We are still willing to have much more improvement and all the consumers are satisfied with the quality of machines offered to you. 【Machine Features】 2 lines coreless star sealed bag on roll making machine Oscillation film feeding & sealing system for stability and high out put Automatically reel changing system High production efficiency to save manpower and time Servo motor, as standard attachment, makes it easy to adjust the bag length and the production speed Computer control over the entire process From film roll to final bag, non-stop, one process flow Automatically stop when running out of film/ film feeding blocks or bags jam/ color scanning misses 【Company Introduction】 COSMO Machinery Co., Ltd. established in March 2001, is well-known for Taiwan manufacturing plastic bag making machinery with servo driving systems. The product from COSMO has the servo motor as standard attachment, makes it easy to adjust the bag length and the production speed, computer control over the entire process, component self-testing function available, high production efficiency to save manpower and time. Up to now, COSMO products are extensively exported to 100 countries spreading all over the world.